105 Jobs in Sligo
Global EHS Auditor
Posted 1 day ago
Job Viewed
Job Description
AbbVie's mission is to discover and deliver innovative medicines and solutions that solve serious health issues today and address the medical challenges of tomorrow. We strive to have a remarkable impact on people's lives across several key therapeutic areas - immunology, oncology, neuroscience, and eye care - and products and services in our Allergan Aesthetics portfolio. For more information about AbbVie, please visit us at Follow @abbvie on X, Facebook, Instagram, YouTube, LinkedIn and Tik Tok ( .
Job Description
We are looking for a Global EHS Auditor who will be responsible for identifying and implementing the strategic approach for the Global Environment, Health and Safety (EHS) auditing program to minimise risk to employees, operations and the environments in which AbbVie operates. This includes providing oversight and direction related to compliance with EHS external regulations and internal policies/procedures worldwide and directly leading the development, implementation, execution and communication of strategies and programs for EHS Auditing.
Roles and Responsibilities
+ Lead Global EHS (GEHS) Audits for the EMEA Region, including but not limited to being main point of contact for audits before, during and after the audit; scheduling audits with locations; pre-audit planning and coordination of pre-audit meetings; audit oversight and support of audit team; leading audit opening meeting, daily update meetings and closing meeting; resolution of any issues that may arise during the audit; preparation and issuing of audit reports and review of subsequent action plans.
+ Manage Global EHS Audit Data within GEHS Management System such as but not limited to; generating EHS audit metrics; trending EHS audit data; reporting of EHS audit data for Global, Sites and Senior Management; and benchmarking data for external industry bodies.
+ Manage all aspects of the Global Environmental, Health, and Safety Auditing Program, which may include the following programs: GEHS Audits, Peer Reviews, Hazardous Waste Vendor Audits, and Third Party EHS Data Assurance Assessments.
+ Conduct program assessments to ensure regulatory and internal compliance as well as consistency of program implementation.
+ Owner and Subject Matter Expert (SME) on GEHS Management and Technical Standards and Procedures as assigned, ensuring that standards and procedures are in place and maintained as appropriate to provide the foundation for standardized company EHS Programs, and to minimize EHS risk.
+ Develop training courses to complement GEHS Technical and Management Standards as appropriate, to enhance understanding of requirements across the enterprise.
+ Develop best-in-class EHS audit practices, framework, approach, policies and enhance EHS compliance through working collaboratively with colleagues across the company and with external stakeholders.
+ Anticipate future trends, obstacles, and barriers as they related to EHS Auditing and develop and implement strategies to address.
+ Execute assigned projects on Global Strategic Long-Range Plan (LRP) efficiently according to schedule and budget.
+ Lead and/or participate in cross functional teams to represent EHS objectives related to the subject matter and to meet the team's overall strategic objectives and deliverables.
+ Scope of position has regional reach, represents company with external organizations, prepares or contributes to reports for regulatory agencies, and minimizes company liability related to EHS impacts.
Travel - Up to 20%.
Qualifications
+ Bachelor's Degree (EHS related, Engineering) plus 10+ years of EHS related experience or Master's Degree (EHS related, Engineering) plus 8-10+ years of EHS related experience.
+ EHS related experience in manufacturing or R&D environment is preferrable.
+ Prior experience in implementing EHS regulations and internal EHS Management/Technical Standards, EHS auditing, conducting incident investigations, interacting with external organisations, and managing cross functional teams.
+ Ability to actively listen, build, and maintain effective working relationships with internal/external colleagues and stakeholders, and resolve conflict.
+ Ability to successfully manage project and programs according to schedule and within approved operational budget.
+ Ability to define scope and magnitude of problem, provide rapid and detailed assessment, coordinate response, present short- and long-term options, and develop procedures to minimise likelihood of re-occurrence.
Additional Information
AbbVie is an equal opportunity employer and is committed to operating with integrity, driving innovation, transforming lives and serving our community? Equal Opportunity Employer/Veterans/Disabled.
US & Puerto Rico only - to learn more, visit & Puerto Rico applicants seeking a reasonable accommodation, click here to learn more:
Manager, Quality Control Projects

Posted 6 days ago
Job Viewed
Job Description
AbbVie's mission is to discover and deliver innovative medicines and solutions that solve serious health issues today and address the medical challenges of tomorrow. We strive to have a remarkable impact on people's lives across several key therapeutic areas - immunology, oncology, neuroscience, and eye care - and products and services in our Allergan Aesthetics portfolio. For more information about AbbVie, please visit us at Follow @abbvie on X, Facebook, Instagram, YouTube, LinkedIn and Tik Tok ( .
Job Description
We are looking for a QC Manager Projects to join our team on our Manorhamilton Road site in Sligo. The QC Manager Projects drives project-related activities within the QC department, focusing on the introduction of innovative analytical techniques, automation, and the transition to a paperless lab environment. This role is pivotal in the implementation of the "Lab of the Future" concept and managing lab expansion projects.
Responsibilities:
+ Lead and manage all project-related activities in the QC department.
+ Oversee the introduction of new analytical techniques, focusing on automation and paperless laboratory systems.
+ Manage the implementation of the Lab of the Future initiative in the QC department.
+ Coordinate and oversee laboratory expansion projects.
+ Manage and oversee compendial reviews, documentation control for QC, maintenance and calibration of analytical instrumentation, analytical work orders on maximo and retain management.
+ Manage purchasing and budget control, including vendor managed inventory, laboratory cleaning services and capital requirements for QC.
+ Manage and ensure delivery of training curricula for QC via laboratory trainer role.
+ Lead operational excellence in QC delivering on various initiatives including reduced testing program for QC.
+ Liaise with PDS&T to ensure execution of reference standard interval testing program.
+ Lead inspection readiness in QC. Participate in internal and external audits and address audit findings.
+ Ensure compliance with data integrity policies and regulatory requirements.
+ Liaise with cross-functional teams to facilitate project goals and timelines.
+ Present project updates and technical data to stakeholders effectively.
+ Report to the Senior QC Manager.
Qualifications
+ M.Sc./B.Sc. in Chemistry or a related discipline.
+ Experience working in API and OSD QC laboratories.
+ Minimum 4 years of experience in people management within a QC lab setting.
+ Strong project management, presentation, and communication skills.
+ Innovative thinking, with a commitment to advancing laboratory practices and compliance.
Additional Information
AbbVie is an equal opportunity employer and is committed to operating with integrity, driving innovation, transforming lives and serving our community? Equal Opportunity Employer/Veterans/Disabled.
US & Puerto Rico only - to learn more, visit & Puerto Rico applicants seeking a reasonable accommodation, click here to learn more:
Operations Supervisor - Monday-Friday Evening Shift
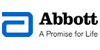
Posted 7 days ago
Job Viewed
Job Description
Abbott is a global healthcare leader that helps people live more fully at all stages of life. Our portfolio of life-changing technologies spans the spectrum of healthcare, with leading businesses and products in diagnostics, medical devices, nutritionals and branded generic medicines. Our 114,000 colleagues serve people in more than 160 countries.
**Abbott in Ireland**
Abbott has been operating in Ireland since 1946 and serves the Irish market with a diverse range of healthcare products including diagnostics, diabetes care, medical devices and nutritional products. In Ireland, Abbott currently employs about 6,000 people across ten sites located in Dublin, Donegal, Clonmel, Cootehill, Galway, Kilkenny, Longford and Sligo.
**Abbott Ireland Nutrition Sligo**
We understand that proper nutrition is the foundation for living the best life possible. That's why we develop science-based nutrition products for people of all ages. Our products help babies and children grow, keep bodies strong and active, and support the unique nutrition needs of people with chronic illnesses - to make every stage of life a healthy one.
Abbott is a leader in providing enteral nutrition feeding devices, including enteral feeding pumps and pump sets. Enteral feeding (also known as tube feeding) is a means of providing nutrition to people who cannot obtain nutrition by swallowing. Enteral nutrition contains all the calories and vitamins a person needs.
**Shift:**
Monday to Thursday 3.30pm to midnight
Friday 2.30pm to 10pm
**Key Responsibilities:**
Reporting to the Operations & Supply Chain Senior Manager, key responsibilities include:
+ Leading some of the following areas and maintain a high-profile presence in the area:
+ Moulding & Extrusion teams plus Warehouse Team
+ Assembly Teams
+ Drive own team and work with other teams to maximize performance.
+ Work with other stakeholders to resolve day to day problems, effect changes in procedures and ramp up line speeds or throughput.
+ Ensure strict compliance with all procedures, regulatory and GMP requirements, quality procedures including record keeping, inspection standards, product disposition and validation protocols.
+ Implement corrective and preventative actions identified through the quality process.
+ Manage your team's time and attendance, including absenteeism/overtime review and occupational health follow-up.
+ Maintain a positive employee relations atmosphere, ensuring that there is good communication and co-operation by encouraging knowledge sharing and open exchange of ideas within the Plant.
+ Take responsibility for training and development of employees on his/her shift. Ensure all employees achieve their full potential and develop their skills to meet the current and future needs of the Operations and Supply Chain Department.
+ Manage team effectively through coaching and counselling where appropriate, leading by example at all times
+ Promote continuous improvement and manage change effectively.
+ Ensure financial performance is maintained at required level with regard to material and labour efficiency.
+ Assist Department Manager and Planners in preparation of schedules.
+ Provide support as required for projects such as:
+ Process development, optimization and validation
+ Material selection and qualification
+ Equipment / mould procurement and introduction
+ Management of capital projects from inception to completion
+ EHS support and compliance within all areas of the dept.
**Supervisory/Management Responsibilities:**
+ General Manufacturing Operators and Process Service Operators will report to the Operations Supervisor
**EHS Responsibilities:**
+ Foster an awareness of Environmental Health & Safety in the plant and promote a culture of continuous improvement.
+ Maintain plant safety at the highest level with a zero accident target
+ Ensure strict compliance with plant environmental, health and safety policies, including:
+ Detailed and timely incident and accident reporting
+ Thorough investigation and corrective action for all hazardous occurrences and accidents and follow-up
**Education Required:**
+ A relevant third-level qualification
**Knowledge:**
+ Proven track record in people management
+ Demonstrated flexible and innovative approach to work
+ At least three years experience in a supervisory role in a GMP Manufacturing/Pharmaceutical/Regulated industry.
+ Good problem-solving, communication, computer analysis and decision-making skills are required.
+ Excellent oral and written communication skills.
+ Good human relations skills in dealing with all levels of employees.
Connect with us at and on LinkedIn , Facebook , Instagram , X and YouTube .
An Equal Opportunity Employer
Abbot welcomes and encourages diversity in our workforce.
We provide reasonable accommodation to qualified individuals with disabilities.
To request accommodation, please call or email
Principal Project Engineer
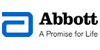
Posted 7 days ago
Job Viewed
Job Description
At Abbott, you will play a crucial role to help people live more fully at all stages of their lives. Abbott is a global healthcare leader, and our portfolio of life-changing technologies spans the spectrum of healthcare, with leading businesses and products in diagnostics, medical devices, nutritional products and branded generic medicines. Our 113,000 colleagues have a daily impact on the life of people in more than 160 countries.
**Abbott Ireland**
In Ireland, Abbott employs around 6,000 people across ten sites. We currently have seven manufacturing facilities located in Clonmel, Cootehill, Donegal, Longford, Sligo & Kilkenny and a third-party manufacturing management operation in Sligo. Abbott also has commercial, support operations and shared services in Dublin and Galway. We have been making a difference in the lives of Irish people since 1946.
**This is how you can make a difference at Abbott:**
We are interested in a **Principal Project Engineer** to lead innovative projects, drive cross-functional collaboration, and shape the future of our technical capabilities.
**Responsibilities:**
+ Lead and execute medium-scale, cross-disciplinary engineering projects with custom, risk-managed plans.
+ Translate customer, business, and technical needs into actionable project scopes and strategies.
+ Conduct feasibility studies and economic analyses to guide decision-making and optimize life cycle costs.
+ Benchmark internally and externally to inform strategic planning and continuous improvement.
+ Design and analyze experiments using diverse data sources to address strategic questions.
+ Develop and implement complete solutions that integrate regulatory, operational, and cost considerations.
+ Ensure quality and effectiveness of key engineering processes through sound design and risk mitigation.
+ Evaluate the impact of design changes and proactively manage potential failure modes.
+ Apply proven methodologies to enhance engineering processes and outcomes.
+ Serve as a technical liaison for internal teams and external stakeholders, including senior leadership.
+ Communicate effectively across various media and organizational levels.
+ Foster collaborative, respectful relationships with colleagues, vendors, and partners.
+ Uphold all Environmental, Health, Safety, and Energy (EHS&E) standards and engineering governance policies.
**Education and Experience:**
+ A Bachelor's degree in Engineering, Science, or a closely related field is preferred. Equivalent technical experience with demonstrated competence will also be considered.
+ A post-graduate degree is desirable and may contribute toward the required experience.
+ A minimum of 6 years of significant engineering and/or operational experience.
+ Proven track record of technical contributions and accomplishments in product or process development.
+ Strong technical knowledge and application of engineering principles and practices.
+ Experience leading and influencing cross-functional teams.
+ Recognized as a subject matter expert in a relevant technical discipline.
+ Background in healthcare, nutritional products, diagnostics, medical devices, pharmaceuticals, or similar industries is advantageous.
+ Demonstrated financial acumen and experience with fiscal control systems.
+ Demonstrated a sound knowledge of injection moulding, tool design, validation activities for medical device components
+ Demonstrated a clear strategy for performance improvements at suppliers for production output, improve quality, support CAPA activities and monitored for effectiveness.
**What we Offer**
Attractive compensation package that includes competitive pay, as well as benefits such as
+ Family health insurance,
+ Excellent pension scheme
+ Life assurance
+ Career Development
+ Fantastic new facility
+ Growing business plus access to many more benefits.
Connect with us at and on LinkedIn , Facebook ( , Instagram , X ( and YouTube .
Abbott is an equal opportunities employer.
An Equal Opportunity Employer
Abbot welcomes and encourages diversity in our workforce.
We provide reasonable accommodation to qualified individuals with disabilities.
To request accommodation, please call or email
Operational Excellence Engineer - Soft Services & Facilities
Posted 7 days ago
Job Viewed
Job Description
At Abbott, you will play a crucial role in helping people live more fully at all stages of their lives. Abbott is a global healthcare leader, and our portfolio of life-changing technologies spans the spectrum of healthcare, with leading businesses and products in diagnostics, medical devices, nutritional products, and branded generic medicines. Our 113,000 colleagues have a daily impact on the lives of people in more than 160 countries. At Abbott, you can shape your career as you help shape the future of healthcare.
**About the Role**
We are looking for a performance-driven professional with a solid background in Operational or Business Excellence and hands-on experience managing soft services within a manufacturing environment. This includes critical support functions such as cleaning, preventive maintenance, pest control, and general facilities upkeep. The ideal candidate combines process optimization skills with an engineering mindset and has a deep understanding of the unique challenges and regulatory expectations associated with soft services in a production setting.
**LOCATIONS: Ireland OR Netherlands & Germany**
**Key Responsibilities**
+ Drive continuous improvement initiatives across soft service operations, ensuring alignment with
+ OPEX/BEX principles
+ Optimize cleaning, sanitation, and facility maintenance processes to improve efficiency, compliance, and cost-effectiveness
+ Develop and implement KPIs to monitor performance of soft services vendors and internal teams
+ Lead audits, root cause analysis, and corrective action planning for deviations in facility hygiene and maintenance standards
+ Collaborate with manufacturing, quality, HSE, and procurement teams to ensure integrated service delivery
+ Lead or support cross-functional projects related to facility upgrades, service outsourcing, or cost reduction
+ Ensure compliance with GMP, EHS, and other relevant regulatory frameworks
+ Provide training and coaching on lean tools and continuous improvement methodologies
**Key Requirements**
+ Degree in Engineering, Facilities Management, or a related technical field
+ 5+ years' experience in manufacturing environments, with a focus on soft services (cleaning, maintenance, sanitation, etc.)
+ Proven track record applying OPEX/BEX or Lean methodologies in facility or support service contexts
+ Strong understanding of regulatory requirements for soft services in GMP or high compliance industries
+ Exceptional stakeholder engagement and vendor management skills
**Preferred Skills**
+ Lean Six Sigma certification (Green or Black Belt)
+ Experience working with outsourced service providers or managing service-level agreements (SLAs)
+ Familiarity with CMMS, CAFM, or other facility management tools
+ Knowledge of ISO standards, GMP, EHS, or similar compliance frameworks
+ Identify and implement cost optimization opportunities within soft services, such as analyzing and improving cleaning effectiveness using metrics like cost per square meter, labor efficiency, and material utilization
**WHAT CAN WE OFFER**
Abbott provides a varied, challenging, and international position in a dynamic and pleasant working environment. In our organization, you can count on excellent primary and secondary benefits, a positive working atmosphere, a personal growth plan, extensive training opportunities and good career perspective. We are in the business of advancement, both in health solutions and in the lives and careers of our employees. Our work across the world and in many areas of healthcare provides a rich environment for our employees to explore career paths, interests and opportunities.
Apply today and Do Work That Matters.
Connect with us at and on LinkedIn , Facebook , Instagram , X and YouTube .
An Equal Opportunity Employer
Abbot welcomes and encourages diversity in our workforce.
We provide reasonable accommodation to qualified individuals with disabilities.
To request accommodation, please call or email
Specialist, Documentation
Posted 13 days ago
Job Viewed
Job Description
AbbVie's mission is to discover and deliver innovative medicines and solutions that solve serious health issues today and address the medical challenges of tomorrow. We strive to have a remarkable impact on people's lives across several key therapeutic areas - immunology, oncology, neuroscience, and eye care - and products and services in our Allergan Aesthetics portfolio. For more information about AbbVie, please visit us at Follow @abbvie on X, Facebook, Instagram, YouTube, LinkedIn and Tik Tok ( .
Job Description
Job Description
AbbVie Manorhamilton Road are looking for a Documentation Specialist to join their team on a 6 month contract. You will be coordinating the development and the maintenance of the AbbVie Laboratory Document Control system in compliance with all applicable company and regulatory requirements.
What you will do:
+ Manage the document management system to ensure compliance with Quality requirements and Regulations.
+ Be responsible for the company Documentation issuance, control and retention ensuring compliance with all policies and procedures.
+ Work closely with the global doc centre and site stakeholders in processing, reviewing and approval process of document change requests
+ Assist with external audits and inspections through coordination, participation and compilation of document packages for audit.
+ Comply with the EHS policy & procedures and demonstrate EHS best practices at all times.
Qualifications
What you will need:
+ 3rd level qualification in a relevant discipline
+ Minimum 2 years in a similar role
+ Previous experience in a GMP environment (pharma would be an advantage)
+ Excellent computer skills, MS office skills essential
Additional Information
AbbVie is an equal opportunity employer and is committed to operating with integrity, driving innovation, transforming lives and serving our community? Equal Opportunity Employer/Veterans/Disabled.
US & Puerto Rico only - to learn more, visit & Puerto Rico applicants seeking a reasonable accommodation, click here to learn more:
Mktg Comm Specialist
Posted 14 days ago
Job Viewed
Job Description
As a Zimmer Biomet team member, you will share in our commitment to providing mobility and renewed life to people around the world. To support our talent team, we focus on development opportunities, robust employee resource groups (ERGs), a flexible working environment, location specific competitive total rewards, wellness incentives and a culture of recognition and performance awards. We are committed to creating an environment where every team member feels included, respected, empowered and recognised.
**Mission ,Tasks and Responsibilities**
The **Digital Marketing Specialist** is responsible for the development, management and maintenance of Zimmer Biomet's various digital marketing channels to help achieve the company's strategic and business objectives. Working closely with internal stakeholders, this person provides the tools, infrastructure and analytics necessary to effectively design and execute digital marketing campaigns, maintain the company's online and social media presence to reach and influence its target audience.
In this role, he/she will conduct the following activities:
- Researches technologies and reviews them for inclusion in the organisation's business promotion plan
- Evaluates and adjusts the performance of the company's digital assets such as zimmerbiomet.com and social media channels
- Research data on competitors, market conditions and customers to improve service delivery
- Plan and control the budget for all digital assets
- Analyse and improve the content, design and functionality of the company's website
- Manage online products and brand campaigns to increase brand awareness
- Oversee digital marketing strategies, such as social media campaigns
- Use SEO and other techniques to improve the company's popularity and online presence
- Designing workable strategies to improve traffic to the company's website and social media channels
Responsibilities in terms of quality and HSE
+ Respect, at his/her level, the procedures, instructions, guidelines, wearing of PPE (Personal Protective Equipment) related to the quality and HSE (Health, Safety and Environment) management system
+ Check, at his/her level, the application of procedures, instructions and guidelines related to the quality and HSE management system.
+ Participate in the continuous improvement of the quality and HSE management system.
+ Report any quality and HSE incidents and implement, at his/her level, corrective and preventive actions to remedy them
**Job Description, Required Skills and Profile**
The **Digital Marketing Specialist** has a degree in digital marketing and has had initial successful experience in a similar role, and has at least a Bachelor's degree in communications, marketing, digital marketing or a related field.
He/she also has the following skills:
- Minimum 3 years' experience in communications and/or digital marketing
- Experience and ability to manage SEO, PPC and email marketing to enhance the company's digital marketing efforts
- Understanding of online marketing best practices, strategies and concepts
- Experience in social media marketing and how to leverage the medium to grow the business
Specialist skills
- Good communication skills, both verbal and written
- Ability to multi-task
- Ability to work accurately and under pressure
- Analytical thinking
- A strong networker
- Ability to work with little or no supervision.
Languages
- English
- Any other language is a plus
Travel conditions: Up to 5% of the total
EOE/M/F/Vet/Disability
Be The First To Know
About the latest All Jobs in Sligo !
Technician, Engineering

Posted 14 days ago
Job Viewed
Job Description
AbbVie's mission is to discover and deliver innovative medicines and solutions that solve serious health issues today and address the medical challenges of tomorrow. We strive to have a remarkable impact on people's lives across several key therapeutic areas - immunology, oncology, neuroscience, and eye care - and products and services in our Allergan Aesthetics portfolio. For more information about AbbVie, please visit us at Follow @abbvie on X, Facebook, Instagram, YouTube, LinkedIn and Tik Tok ( .
Job Description
What you do, is what we need. Making a difference begins here. And takes all of us.
Welcome to AbbVie!
We are a global, research-based biopharmaceutical company that combines the focus and passion of leading-edge biotech with the expertise and capability of an established pharmaceutical leader. Redefining what is possible is our business and our passion. Our goal is to help patients live healthier lives and we are proud to be a Great Place to Work.
Purpose:
The purpose of this role is to provide a Manufacturing Engineering service to the plant, in order to maximise the availability of our Manufacturing Equipment. You will also ensure the performance of day to day preventative, predictive and demand maintenance activity to maintain manufacturing and utilities equipment. This role is based on our Manorhamilton Road site on a 12 month contract.
Flexibility to work shifts that include Days & Nights is essential for this role.
Responsibilities:
+ To liaise with Production to ensure equipment performance is maximized.
+ To maintain records and documentation on relevant Engineering Procedures and preventative & demand maintenance.
+ To liaise with Internal/External Engineering personnel and contract maintenance providers in maintaining, troubleshooting and installing/commissioning equipment.
+ To facilitate the implementation of equipment projects/ process improvements.
+ Establish with the engineering team leader the department goals, schedules and timetables for activities.
+ Contribute to successful external, Division and Corporate audits.
+ Identification and implementation of manufacturing equipment related cost improvement plans and continuous improvement plans.
+ Cross train within manufacturing engineering.
+ Ensure safety standards are met and safe working practices adhered to.
+ Support the Production Team in ensuring that manufacturing equipment is maintained to meet the output and yield requirements.
+ Adhering to all relevant policies relating to Quality and regulatory
+ Supervision of external contractors carrying out work onsite
+ Required to undertake specific investigations, and equipment monitoring, with the view to improve manufacturing performance e.g. reducing plant, maximizing output and yield.
+ Optimisation of elements of manufacturing machinery to adapt to process conditions in order to improve efficiency.
+ Considerable and continual care and attention needed to avoid substantial damage to equipment
+ Adherence to the MEP (Maintenance Excellence Programme) is required to ensure increased reliability and decreased downtime for the plant.
Business Skills
+ Requires a high level of attention to detail and mental concentration, to ensure accuracy and total compliance with procedures at all times.
+ Requires proven problem-solving skills and the ability to adapt to new regulatory requirements.
+ Must be results driven striving to meet all targets and metric standards as set by site/department and division leaders.
+ Strong communication skills both verbal and written are required for the execution of this role.
+ Strong interpersonal skills are required.
+ Demonstrates an ethos of Right First Time at all times.
+ Each Engineering Technician is responsible for their own work and the execution of their tasks on a daily basis.
+ Candidates must be flexible and support the business through working a 24 x 7 shift roster and on call rota as required.
Qualifications
What you will need:
+ 3rd level qualification in an Engineering discipline
+ Trade qualified will also be considered
+ 3-5 years experience in a regulated environment (GMP preferable)
+ Strong IT knowledge is required.
+ Strong trouble shooting and documentation skills
Additional Information
AbbVie is an equal opportunity employer and is committed to operating with integrity, driving innovation, transforming lives and serving our community? Equal Opportunity Employer/Veterans/Disabled.
US & Puerto Rico only - to learn more, visit & Puerto Rico applicants seeking a reasonable accommodation, click here to learn more:
Abbott Professional Development Program Operations (OPDP) - Ireland
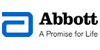
Posted 15 days ago
Job Viewed
Job Description
We currently have a number of open positions on our OPDP Program in Ireland.
Upon completion, PDP participants graduate into their next full-time position in their home country, continuing to grow their career and contributing as an Abbott professional using the foundation of skills, experience and network developed during their time in the program.
**As a OPDP participant you will:**
· Be a regular full-time employee of Abbott and qualify for the same competitive salary and benefits as other Abbott employees.
· Assume full responsibility and contribute as a functional operation professional.
· Rotate through three challenging, demanding, and diverse assignments.
· Develop a well-rounded skill set through assignments in the established learning tracks (see below) for the program.
· Relocate to various sites around Ireland to experience assignment diversity and operations
· Work within multiple business units during your rotational program at Abbott.
· Have the opportunity to explore possible crossover assignments within other Operation Programs (i.e. Engineering, Manufacturing, Quality, Operational Excellence).
· Be paired with a mentor to assist in the development of your operations career.
· Create a personalized growth plan to serve as a step-by-step guide towards the experiences, knowledge, and resources necessary to achieve your career goals
· Obtain training customized to support your individual growth and development.
· Report to a department manager in each assignment who will oversee your day-to-day responsibilities.
**OPDP rotation overview:**
· In Ireland, the OPDP rotation is based on 12month rotations in the first two of three years. Your rotations will involve working across functional areas - Technical, Operations Planning, Quality Assurance, Project Management and Engineering.
· No assignment is repeated; each is with a different Assignment Manager
· OPDP participants starting the program in July 2026 will complete a three-year program with the final international (overseas) rotation ending in June 2029
**Requirements:**
+ Bachelor's Degree/master's in Engineering?(Automation / Mechanical / Electrical / ?Automation) Biotechnology, Pharmacy, Food Science, Supply Chain (Business Studies with major/minor Supply Chain) or related disciplines (grade 2:1 or higher)
+ Tracking to or have a minimum of 2.1 Grade in your undergraduate course with a track record of outstanding co-curricular activities
+ Interest in pursuing a career in Operations - Production, Engineering, Plant Quality, etc.
+ Geographically mobile and willing to do at least one year assignment outside of home country
+ Unrestricted authorization to work in home country (within Europe)
+ Fluent level of English for written and verbal business communication.
**Key Skills**
+ Cpacity to apply skills and knowledge to address operational challenges and add value to the business.
+ Strong analytical and problem-solving skills.
+ Strong interpersonal, leadership & communication skills.
+ Eager to learn and has the flexibility and willingness to work on different projects.
+ Previous work experience in internship or co-op work experience would be an advantage
The closing date for applications is **Friday, 10 October 2025** . However, interviews will be conducted on a rolling basis from the launch of the program. We strongly encourage students to apply as early as possible to avoid missing out on these exciting opportunities.
#earlycareers
An Equal Opportunity Employer
Abbot welcomes and encourages diversity in our workforce.
We provide reasonable accommodation to qualified individuals with disabilities.
To request accommodation, please call or email
Specialist, NPI Compliance
Posted 15 days ago
Job Viewed
Job Description
AbbVie's mission is to discover and deliver innovative medicines and solutions that solve serious health issues today and address the medical challenges of tomorrow. We strive to have a remarkable impact on people's lives across several key therapeutic areas - immunology, oncology, neuroscience, and eye care - and products and services in our Allergan Aesthetics portfolio. For more information about AbbVie, please visit us at Follow @abbvie on X, Facebook, Instagram, YouTube, LinkedIn and Tik Tok ( .
Job Description
More than a job - It's a chance to make a real difference
Working at AbbVie is more than a job. It's a career with meaning. A chance to make a difference, in the world and in your life.
We are recruiting for a NPI Compliance Specialist to join the team based in AbbVie Manorhamilton, Sligo on a Fixed Term Contract. The NPI Compliance Specialist is responsible for ensuring new products transferred to AbbVie Sligo are manufactured in accordance with applicable regulatory requirements and AbbVie procedures and policies. To ensure effective and compliant transfer of New Products to the site.
Responsibilities:
+ Taking responsibility for maintaining the effectiveness of the integration of new products into the AbbVie NPI quality system.
+ Ensuring that new products manufactured at AbbVie Ireland NL B.V. meet requirements of applicable regulatory requirements and AbbVie procedures and policies.
+ Be responsible for supporting new product transfers to the site from development through to commercialization, liaising closely with local and external cross functional teams to provide direction on quality concerns and ensure appropriate mitigation to address potential risk.
+ Supporting vendor evaluation and approval, management of all technical agreements from initiation, review, approval, and storage.
+ Supporting review and approval of NPI related Analytical Test Method Transfers and / or validation.
+ Collaborating with CMC QA, R&D, S&T, and other functional groups to maintain roles and responsibilities, identify potential quality issues, obtain an understanding of the quality compliance and provide input on quality concerns.
+ Coordination of site review of new product related material specification documents including but not limited to, intermediate specifications, API specifications, Drug Product specifications, raw material specifications, and excipient specifications.
+ Supporting review and approval of new product related analytical Test Method Transfers and/or validation.
+ Supporting the management of new product related exception documentation including the generation of corrective and preventative action to prevent reoccurrence.
+ Generation of product transfer documentation to attest the completion of product transfer deliverables, in advance of the applicable product transfer stage gate review.
+ Interfaces with internal auditors and outside regulatory agencies/auditors as the subject matter expert for new products and technology transfers.
+ Adheres to and supports all EHS & E standards, procedures and policies.
Qualifications
What you will need:
+ A third level qualification in a science or quality discipline
+ Minimum 3 years' Experience in Pharmaceutical or Sterile Manufacturing environment
+ Strong written and verbal communication skills
+ Strong work ethic
Additional Information
AbbVie is an equal opportunity employer and is committed to operating with integrity, driving innovation, transforming lives and serving our community? Equal Opportunity Employer/Veterans/Disabled.
US & Puerto Rico only - to learn more, visit & Puerto Rico applicants seeking a reasonable accommodation, click here to learn more: